Alloy refers to a solid product with metallic properties obtained after a metal and another or several metals or non-metals are mixed and melted, and then cooled and solidified.
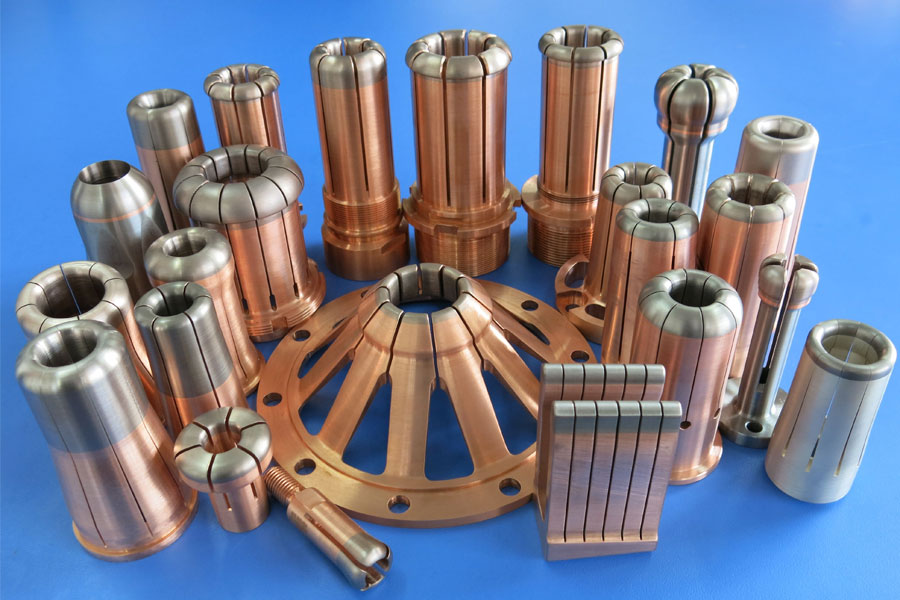
What Is An Alloy?
Alloy is a substance with metallic characteristics synthesized by a certain method from two or more metals and metals or non-metals. It is generally obtained by melting into a homogeneous liquid and solidifying. According to the number of constituent elements, it can be divided into binary alloys, ternary alloys and multi-element alloys.
The production of alloys by mankind began with the production of bronzes. The Babylonians were the first to produce alloys in the world. The Babylonians began to refine bronze (alloy of copper and tin) 6000 years ago. China is also one of the earliest countries in the world to research and produce alloys. In the Shang Dynasty (more than 3000 years ago), the bronze (copper-tin alloy) process was very developed; about the 6th century BC (late Spring and Autumn period), it was forged (remaining Heat-treated) a sharp sword.
Alloys are macroscopically uniform, diversified substances containing metal elements, and generally have metal characteristics. Any element can be used as alloying elements, but a large amount of added is still metal. The most basic and independent substances that make up an alloy are called components, or Abbreviated as yuan. An alloy composed of two components is called a binary alloy, an alloy composed of three components is called a ternary alloy, and an alloy composed of more than three components is called a multi-element alloy. In the solid state, an alloy It may be a single phase or a mixture of multiple phases; it may be crystalline, or it may be quasicrystalline or amorphous. The difference in crystalline alloys depends on the atomic radius, electronegativity, and electron concentration of its constituent elements. The possible phases are solid solutions that maintain the same structure as the pure element of the substrate and inter-mediate phases that do not have the same structure as any constituent elements. Intermediate phases include normal valence compounds, electronic compounds, laves phases, σ phases, interstitial phases and interstitial compounds with complex structures, etc. The possible phases of the alloy in the equilibrium state can be known from the phase equilibrium diagram.
The structure and properties of the constituent phases in the alloy play a decisive role in the performance of the alloy. At the same time, the changes in the alloy structure, namely the relative number of phases in the alloy, the changes in the grain size, shape and distribution of the phases, also affect the performance of the alloy. Great influence. Therefore, the combination of various elements to form a variety of different alloy phases, and then through appropriate treatment may meet a variety of different performance requirements.
The term alloy is now also used in polymer chemistry, which refers to a composite material made by blending a polymer or copolymer with another polymer or elastomer under certain conditions, such as styrene-acrylonitrile copolymer resin Blended with butadiene-acrylonitrile rubber
The Make Synthesis Of Alloy
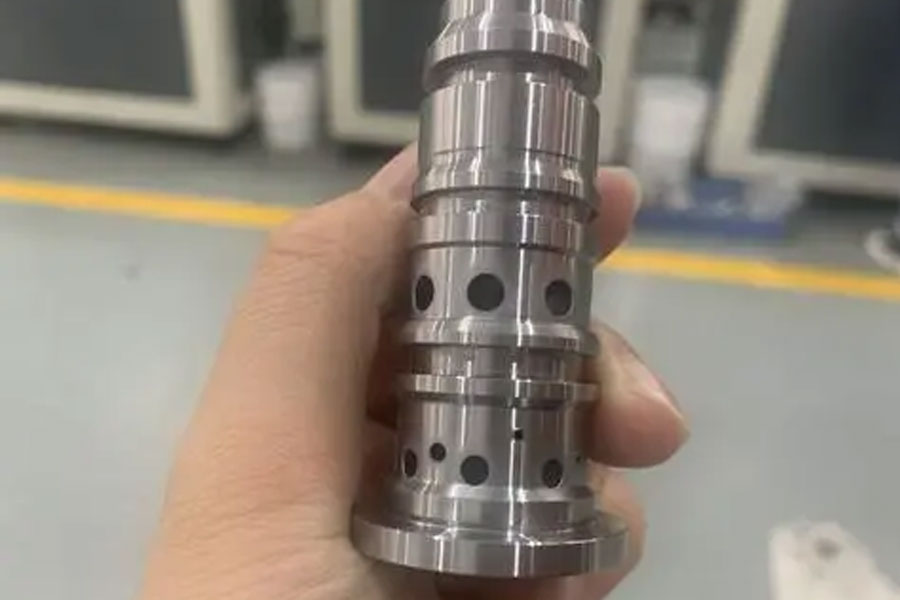
Metallic materials with metallic characteristics are often formed by two or more metal elements or metal-based addition of other non-metal elements through alloying processes (melting, mechanical alloying, sintering, vapor deposition, etc.) are called alloys . But the alloy may only contain one metal element, such as steel. (Steel is the general term for ferroalloys with carbon content between 0.02% and 2.00% by mass)
Here we need to note that the alloy is not a general conceptual mixture, or even a pure substance, such as a single-phase intermetallic compound alloy. The added alloying elements can form solid solutions, compounds, and produce endothermic or exothermic reactions, thereby changing the metal. The nature of the matrix.
The formation of alloys often improves the properties of elemental elements. For example, the strength of steel is greater than that of its main constituent element, iron. The physical properties of the alloy, such as density, reactivity, Young’s modulus, electrical conductivity and thermal conductivity, may be similar to the constituent elements of the alloy, but the tensile strength and shear strength of the alloy are usually related to the properties of the constituent elements. with large differences. This is because the arrangement of atoms in the alloy and the element is very different.
A small amount of a certain element may have a great influence on the properties of the alloy. For example, impurities in ferromagnetic alloys can change the properties of the alloy.
Unlike pure metals, most alloys do not have a fixed melting point. When the temperature is within the melting temperature range, the mixture is in a state of coexistence of solid and liquid. Therefore, it can be said that the melting point of the alloy is lower than that of the component metal. See eutectic mixture. Among the common alloys, brass is an alloy of copper and zinc; bronze is an alloy of tin and copper, used for statues, ornaments and church bells. Some currencies use alloys (such as nickel alloys).
The Physical Classification Of Alloy
According to the name of the main metal in the alloy, it is classified as a certain alloy. For example, the copper alloy with high copper content is mainly used to maintain the performance of copper.
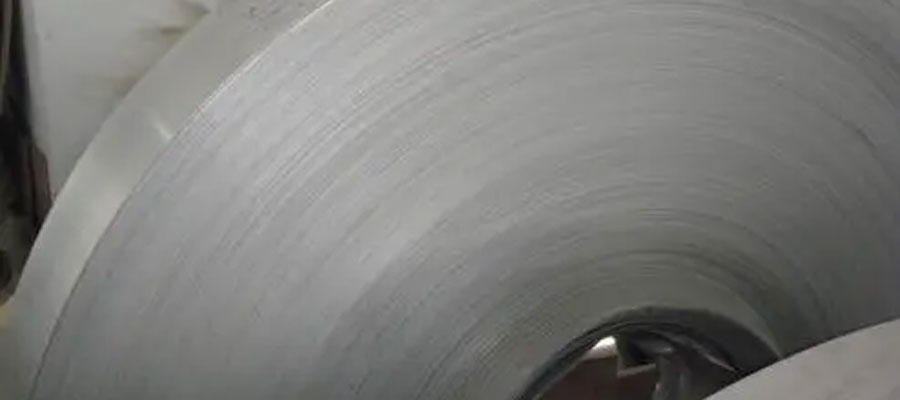
Alloy Type
- Mixed alloy (eutectic mixture), when the liquid alloy is solidified, the alloys formed by the respective components of the alloy crystallized, such as solder, bismuth-cadmium alloy, etc.;
- Solid solution alloys, which form solid solutions when liquid alloys are solidified, such as gold and silver alloys;
- Intermetallic compound alloys, alloys in which each component forms a compound with each other, such as brass (β-brass, γ-brass and ε-brass) composed of copper and zinc.
Many properties of alloys are better than pure metals, so alloys are mostly used in application materials (see ferroalloys, stainless steel).
The Generality Of The Alloy
All types of alloys have the following common features:
- The melting point of most alloys is lower than the melting point of any one of its constituent metals;
- The hardness is generally greater than the hardness of any metal in its component; (Special case: sodium potassium alloy is liquid and used as a heat transfer agent in atomic reactors)
- The electrical and thermal conductivity of the alloy is lower than that of any component metal. Using this characteristic of the alloy, high resistance and high thermal resistance materials can be manufactured. Materials with special properties can also be manufactured.
- Some have strong corrosion resistance (such as stainless steel). For example, 15% chromium and 9% nickel are added to iron to obtain a corrosion-resistant stainless steel, which is suitable for the chemical industry.
Common Alloys
Ductile iron, manganese steel, stainless steel, brass, bronze, cupronickel, solder, duralumin, 18K gold, 18K white gold, etc.
1.Steel Alloy
Introduction
Steel is an alloy composed of iron and C, Si, Mn, P, S and a small amount of other elements. In addition to Fe, the content of C plays a major role in the mechanical properties of steel, so it is collectively referred to as iron-carbon alloy. It is the most important and most used metal material in engineering technology.
Classification and nature
According to the different carbon content, iron-carbon alloys are divided into two categories: steel and pig iron. Steel is an iron-carbon alloy with a carbon content of 0.03% to 2%. Carbon steel is the most commonly used ordinary steel. It is easy to smelt, easy to process, low in price, and can meet the requirements of use in most cases, so it is widely used. According to different carbon content, carbon steel is divided into low carbon steel, medium carbon steel and high carbon steel.
As the carbon content increases, the hardness of carbon steel increases and the toughness decreases. Alloy steel is also called special steel. One or more alloy elements are added on the basis of carbon steel to have some special properties, such as high hardness, high wear resistance, high toughness, corrosion resistance, and so on. The alloying elements often added to steel are Si, W, Mn, Cr, Ni, Mo, V, Ti, etc. The resources of alloy steel in my country are quite abundant. Except for Cr and Co insufficient and low Mn grade, the reserves of W, Mo, V, Ti and rare earth metals are all high.
2.Pig Iron Alloy
Pig iron is hard and brittle, but resistant to pressure and wear. Gray iron and ductile iron. The carbon in white iron is silver-white in Fe3C fracture, hard and brittle, and cannot be machined. It is the raw material for steelmaking, so it is also called steelmaking pig iron.
Carbon distributed in the form of flake graphite is called gray iron, with a silver-gray fracture, which is easy to cut, easy to cast, and wear-resistant. If the carbon is distributed in spheroidal graphite, it is called nodular cast iron, and its performance and processing performance are close to steel. Special alloy elements can be added to cast iron to obtain special cast iron. If Cr is added, the wear resistance can be greatly improved, and it has very important applications under special conditions.
3.Ferrosilicon Alloy
Ferrosilicon is made by smelting coke, steel scraps, and quartz (or silica) in an electric furnace. Silicon and oxygen are easily synthesized into silicon dioxide. Therefore, ferrosilicon is often used as a deoxidizer in steelmaking. At the same time, since SIO2 generates a lot of heat, it is also beneficial to increase the temperature of molten steel while deoxidizing. Ferrosilicon is used as an alloying element additive.
It is widely used in low-alloy structural steel, composite steel, spring steel, bearing steel, heat-resistant steel and electrical silicon steel. In addition, ferrosilicon is often used as a reducing agent in ferroalloy production and chemical industry. The silicon content is 95%–99%. Pure silicon is commonly used to manufacture single crystal silicon or to prepare non-ferrous metal alloys.
4.Ferromanganese Alloy
Ferromanganese is made from manganese ore. Smelted in a blast furnace or electric furnace. Ferromanganese is also a commonly used deoxidizer in steel, and manganese can also desulfurize and reduce the harmful effects of sulfur. Therefore, almost all kinds of steel and cast iron contain a certain amount of manganese. Ferromanganese is also used as an important alloying agent. Widely used in structural steel. Tool steel, stainless heat-resistant steel. In alloy steel such as wear-resistant steel.
5.Aluminum alloy
Introduction
Aluminum is a widely distributed element, and its content in the earth’s crust is second only to oxygen and silicon, and is the highest content in metals. Pure aluminum has a low density of 2.7 g/cm3, good thermal and electrical conductivity (second only to Au, Ag, Cu), good ductility and high plasticity, and can be processed by various machining. The chemical properties of aluminum are active, and it oxidizes rapidly in the air to form a dense and firm oxide film, which has good corrosion resistance. However, the strength of pure aluminum is low, and only through alloying can various aluminum alloys that can be used as structural materials be obtained.
Features and properties
The outstanding features of aluminum alloy are low density and high strength. The Al-Mn and Al-Mg alloys formed by adding Mn and Mg to aluminum have good corrosion resistance, good plasticity and high strength. They are called anti-rust aluminum alloys. They are used to make fuel tanks, containers, pipes, and rivets. Wait. The strength of hard aluminum alloy is higher than that of rust-proof aluminum alloy, but the corrosion resistance is reduced. There are Al-Cu-Mg series and Al-Cu-Mg-Zn series of such alloys. The newly developed high-strength duralumin has further improved its strength, and its density is 15% lower than that of ordinary duralumin. It can be extruded and can be used as components such as motorcycle frames and rims. Al-Li alloy can be used to make aircraft parts and advanced sports equipment that can withstand heavy loads.
Application
High-strength aluminum alloys are widely used in the manufacture of aircraft, ships and trucks, which can increase their load capacity and speed, and are resistant to seawater erosion and magnetism.
6.Copper alloy
Introduction
Pure copper is purple-red, so it is also called red copper. It has excellent thermal and electrical conductivity. Its electrical conductivity is second only to silver and ranks second among metals. Copper has excellent chemical stability and corrosion resistance, and is an excellent electrical metal material.
Classification
Copper alloys widely used in industry include brass, bronze and cupronickel.
The alloy of Cu and Zn is called brass, in which Cu accounts for 60% to 90% and Zn accounts for 40% to 10%. It has excellent thermal conductivity and corrosion resistance and can be used as various instrument parts. Another example is the addition of a small amount of Sn to brass, which is called navy brass, which has good resistance to seawater corrosion.
A small amount of lubricating Pb is added to brass, which can be used as a sliding bearing material.
Bronze is the metal material with the longest history of use by mankind. It is an alloy of Cu and Sn. The addition of tin significantly increases the strength of copper, improves its plasticity, and enhances its corrosion resistance. Therefore, tin bronze is often used to manufacture gears and other wear-resistant parts and corrosion-resistant accessories. Sn is more expensive, and a series of bronze alloys have been obtained by replacing Sn with Al, Si, and Mn in large quantities. Aluminum bronze has better corrosion resistance than tin bronze. Beryllium bronze is the strongest copper alloy. It is non-magnetic and has excellent corrosion resistance. It is a spring material that can compete with steel.
Cupronickel is a Cu-Ni alloy with excellent corrosion resistance and high electrical resistance, so it can be used as a material for parts and resistors that work under harsh corrosive conditions.
Brass contains zinc and a small amount of tin, lead, aluminum, etc.
7.Zinc alloy
Introduction
An alloy composed of other elements based on zinc. Commonly added alloying elements are aluminum, copper, magnesium, cadmium, lead, titanium and so on. Zinc alloy has a low melting point, good fluidity, easy to weld, braze and plastic process, corrosion resistance in the atmosphere, and easy recycling and remelting of residual waste; but its creep strength is low and natural aging is easy to cause dimensional changes. Prepared by melting method, die-casting or pressure-processed into material. According to the manufacturing process, it can be divided into cast zinc alloy and wrought zinc alloy.
Application and others
The main added elements of zinc alloys are aluminum, copper and magnesium. Zinc alloys can be divided into deformation and cast zinc alloys according to the processing technology. Cast zinc alloys have good fluidity and corrosion resistance, and are suitable for die-casting instruments and auto parts shells. Wait.
Characteristics of zinc alloy
- Proportionality.
- Good casting performance, it can die-cast precision parts with complex shapes and thin walls, and the surface of the castings is smooth.
- Surface treatment: electroplating, spraying, painting.
- When melting and die-casting, it does not absorb iron, does not corrode the profiling, and does not stick to the mold.
- It has good mechanical properties and abrasion resistance at room temperature.
- Low melting point, melting at 385℃, easy to die-casting.
8.Pewter Alloy
classification
Lead-tin alloy is divided into:
- Lead-based or tin-based bearing alloys. Collectively referred to as Babbitt alloy with lead-based bearing alloy. Contains 3% to 15% antimony, 3% to 10% copper, and some alloy varieties also contain 10% lead. Antimony and copper are used to improve the strength and hardness of the alloy. Its friction coefficient is small, and it has good toughness, thermal conductivity and corrosion resistance. It is mainly used to manufacture sliding bearings.
- Lead-tin solder. Mainly tin-lead alloy, and some tin solder also contains a small amount of antimony. Tin alloy containing 38.1% of lead is commonly known as solder, with a melting point of about 183°C. It is used for welding components in the electrical instrument industry, as well as for sealing automobile radiators, heat exchangers, and food and beverage containers.
- Pb-tin alloy coating. Utilizing the anti-corrosion properties of tin alloy, it is coated on the surface of various electrical components, which is both protective and decorative. Commonly used are tin-lead series, tin-nickel coatings and so on.
- Pewter alloys (including pewter alloys and lead-free tin alloys) can be used to produce various exquisite alloy jewelry and alloy crafts, such as rings, necklaces, bracelets, earrings, brooches, buttons, tie clips, hat decorations, and craft pendulums. Ornaments, alloy photo frames, religious emblems, miniature statues, souvenirs, etc.
Features
The characteristics of lead-tin alloy (used as alloy jewelry, alloy handicraft material)
- Lead-tin alloy has stable performance, low melting point, good fluidity and low shrinkage.
- The lead-tin alloy has fine grains, good toughness, suitable hardness and softness, smooth surface, no sand holes, no defects, no cracks, and good polishing and electroplating effects.
- Lead-tin alloy centrifugal casting has good performance and strong toughness. It can cast precision parts with complex shapes and thin walls, and the surface of the castings is smooth.
- Lead-tin alloy products can be surface treated: electroplating, spraying, painting.
- The lead-tin alloy crystal structure is compact, and the raw material ensures that the castings have small dimensional tolerances, exquisite surfaces, and few post-processing defects.
Special Alloy
There are thousands of alloys used in industry, and only a few of them are briefly introduced.
1.Corrosion Resistant Alloy
The ability of metal materials to resist corrosion in corrosive media is called the corrosion resistance of metals. Pure metals with high corrosion resistance usually meet one of the following three conditions:
- Metals with high thermodynamic stability. It can usually be judged by its standard electrode potential. The more positive value has higher stability; the more negative value has lower stability. Noble metals with good corrosion resistance, such as Pt, Au, Ag, Cu, etc. belong to this category.
- Metal that is easy to passivate. Many metals can form a protective dense oxide film in the oxidizing medium. This phenomenon is called passivation. Among metals, the most easily passivated are Ti, Zr, Ta, Nb, Cr and Al.
- The surface can generate insoluble and good protective corrosion product film metal. This situation only occurs when the metal is in a specific corrosive medium, such as Pb and Al in H2SO4 solution, Fe in H3PO4 solution, Mo in hydrochloric acid, and Zn in the atmosphere.
Therefore, in the industry, according to the above principles, a series of corrosion-resistant alloys are obtained by alloying methods, and there are generally three corresponding methods:
- Improve the thermodynamic stability of the metal or alloy, that is, add alloy elements with high thermodynamic stability to the original non-corrosive metal or alloy to form a solid solution and increase the electrode potential of the alloy to enhance its corrosion resistance. For example, adding Au to Cu, adding Cu, Cr, etc. to Ni, is of this type. However, this method of adding precious metals in large quantities has limited applications in industrial structural materials.
- Adding easily passivating alloy elements, such as Cr, Ni, Mo, etc., can improve the corrosion resistance of the base metal. Adding an appropriate amount of Cr to the steel can produce chromium-based stainless steel.Experiments have proved that in stainless steel, the Cr content should generally be greater than 13% before it can play a role in corrosion resistance. The higher the Cr content, the better the corrosion resistance. This type of stainless steel has good corrosion resistance in oxidizing media, but it has poor corrosion resistance in non-oxidizing media such as dilute sulfuric acid and hydrochloric acid. This is because the non-oxidizing acid is not easy to cause the alloy to form an oxide film, and it also has a dissolving effect on the oxide film.
- The addition of alloying elements that can promote the formation of a dense corrosion product protective film on the alloy surface is another way to prepare corrosion-resistant alloys. For example, steel can withstand atmospheric corrosion due to the formation of densely structured compound iron oxyhydroxide [FeOx·(OH)23-2x] on its surface, which can play a protective role. The addition of Cu and P or P and Cr to the steel can promote the formation of this protective film. Therefore, Cu, P, P, and Cr can be used to make atmospheric corrosion-resistant low-alloy steel.
Metal corrosion is the most harmful spontaneous process in industry, so the development and application of corrosion-resistant alloys have great social significance and economic value.
2.Heat resistant alloy
Heat-resistant alloy alloys are also called superalloys, which are of great significance to the industrial sector and application technology fields under high temperature conditions.
Generally speaking, the higher the melting point of the metal material, the higher the temperature limit it can be used. This is because as the temperature increases, the mechanical properties of metal materials decrease significantly, and the tendency of oxidation and corrosion increases accordingly. Therefore, general metal materials can only work for a long time at 500 ℃ to 600 ℃. Metals that can work at high temperatures higher than 700 ℃ are generally called heat-resistant alloys. “Heat resistance” means that it can maintain sufficient strength and good oxidation resistance at high temperatures.
There are two ways to improve the oxidation resistance of steel: one is to add alloying elements such as Cr, Si, Al to the steel, or to carry out Cr, Si, Al alloying treatment on the surface of the steel. They can quickly form a dense oxide film in an oxidizing atmosphere, and firmly adhere to the surface of the steel, thereby effectively preventing the oxidation from proceeding. The second is to use various methods to form high-melting-point oxides, carbides, nitrides and other high-temperature coatings on the surface of steel.
There are many ways to improve the high-temperature strength of steel. From the chemical point of view of structure and properties, there are roughly two main methods:
One is to increase the bonding force between atoms in steel at high temperatures. Studies have pointed out that the bonding force in metals, that is, the strength of metal bonds, is mainly related to the number of unpaired electrons in the atom. From the periodic table, the metal bond of element VIB is the strongest in the same period. Therefore, adding Cr, Mo, W and other atoms to steel has the best effect.
The second is to add elements that can form various carbides or intermetallic compounds to strengthen the steel matrix. The carbides formed by a number of transition metals and carbon atoms are interstitial compounds. They add covalent bonds to the metal bonds, so they have extremely high hardness and high melting points. For example, adding W, Mo, V, and Nb can generate carbides such as WC, W2C, MoC, Mo2C, VC, and NbC, thereby increasing the high temperature strength of steel.
Using alloy methods, in addition to iron-based heat-resistant alloys, nickel-based, molybdenum-based, niobium-based and tungsten-based heat-resistant alloys can also be prepared, which have good mechanical properties and chemical stability at high temperatures. Among them, nickel-based alloy is the best super heat-resistant metal material. The matrix in the structure is a solid solution of Ni?Cr?Co and Ni3Al metal compound. After treatment, its use temperature can reach 1,000 ℃ to 1 100 ℃.
3.Titanium alloy
Titanium is the IVB element in the periodic table. It looks like steel and has a melting point of 1 672 ℃. It is a refractory metal. Titanium is abundant in the earth’s crust, much higher than common metals such as Cu, Zn, Sn, and Pb. my country’s titanium resources are extremely rich. Only among the super-large vanadium-titanium magnetites discovered in Panzhihua, Sichuan, the associated titanium metal reserves are approximately 420 million tons, which is close to the total proven titanium reserves abroad.
Pure titanium has strong mechanical properties, good plasticity, and easy processing. If impurities, especially O, N, and C, increase the strength and hardness of titanium, but will reduce its plasticity and increase brittleness.
Titanium is a metal that is easily passivated, and in an oxygen-containing environment, its passivation film can heal itself after being damaged. Therefore, dry corrosive media are stable. Titanium and titanium alloys have excellent corrosion resistance and can only be corroded by the concentration of hydrofluoric acid. Especially stable, after taking out the titanium or titanium alloy, it is still bright as before, far better than stainless steel.
Another important characteristic of titanium is its low density. Its strength is 3.5 times that of stainless steel and 1.3 times that of aluminum alloy, which is the highest among all industrial metal materials.
Liquid titanium can dissolve almost all metals and form various alloys such as solid solutions or metal compounds. The addition of alloying elements such as Al, V, Zr, Sn, Si, Mo and Mn can improve the properties of titanium to meet the needs of different departments. For example, Ti-Al-Sn alloy has high thermal stability and can work for a long time at a relatively high temperature; superplastic alloy represented by Ti-Al-V alloy can be extended by 50% to 150% Processing and forming, its maximum elongation can reach 2 000%. The elongation of general alloy plastic working is no more than 30%.
Due to the above-mentioned excellent properties, titanium enjoys the reputation of “the metal of the future”. Titanium alloy has been widely used in various sectors of the national economy. It is an indispensable material for rockets, missiles and space shuttles. Titanium alloys are widely used in ships, chemicals, electronic devices and communication equipment, as well as in some light industry sectors. However, the price of titanium is relatively expensive, which limits its widespread use.
4.Magnetic Alloy
In the external magnetic field, the material can show three situations:
- What is not attracted by the magnetic field is called diamagnetic material;
- Those that are weakly attracted by the magnetic field are called paramagnetic materials;
- The ferromagnetic materials that are strongly attracted by the magnetic field are called ferromagnetic materials, and their magnetic properties increase sharply with the strengthening of the external magnetic field, and they can still retain the magnetism after the external magnetic field is removed.
Among the metal materials, most transition metals are paramagnetic; only a few metals such as Fe, Co, and Ni are ferromagnetic. The main elements that make up permanent magnet materials in metals are Fe, Co, Ni and some rare earth elements. The permanent magnet alloys used are rare earth-cobalt-based, iron-chromium-cobalt-based and manganese-aluminum-carbon alloys.
Magnetic alloys are increasingly widely used in emerging technologies such as electric power, electronics, computers, automatic control, and electro-optics.
5.Sodium Potaddium Al
- 【Chemical structure】4K-Na
- 【Chemical characteristics】Silver soft solid or liquid. It reacts violently when exposed to acid, carbon dioxide, moisture and water, and releases hydrogen. It ignites immediately and sometimes even explodes. Density: 0.847g/ml (100℃) (K78%, Na22) %); 0.886 g/ml (100°C) (K56%, Na44%) Melting point: -11°C (K78%, Na22%); 19°C (K56%, Na44%);
- 【Limit parameters】Boiling point: 784°C (K78%, Na22%); 825°C (K56%, Na44%);
[Application] The coolant used in liquid metal nuclear reactors is sodium-potassium alloy, which is liquid at room temperature.
Melting point of sodium potassium alloy
- 20% 80% -10 ℃
- 22% 78% -11 ℃
- 24% 76% -3.5 ℃
- 40% 60% 5 ℃
New Alloy
With the development of science and technology, the types of new alloys are increasing. Here are the main ones.
1.Lightweight alloy
Aluminum-lithium alloy has the characteristics of high specific strength (breaking strength/density), high specific rigidity and low relative density. If used as a modern aircraft skin material, a large passenger aircraft can reduce the weight by 50 kg. Take the Boeing 747 as an example. For every 1 kg lightened, a profit of US$2,000 can be made a year. Titanium alloy is lighter than steel, corrosion resistant, non-magnetic, and high in strength. It is an ideal material for aviation and naval vessels.
2.Hydrogen storage alloy
Due to the limited reserves of oil and coal, and environmental pollution and other problems in the use process, especially the global oil crisis in the 1970s, hydrogen energy has become a research hotspot as a new clean fuel. In the process of hydrogen energy utilization, the storage and transportation of hydrogen is an important link. In 1969, the Dutch Philips company developed the LaNi5 hydrogen storage alloy, which has a large amount of reversible absorption and release of hydrogen. The density of hydrogen in the alloy hydride LaNi5H6 is equivalent to that of liquid hydrogen, which is about 1,000 times the density of hydrogen.
Hydrogen storage alloy is an alloy composed of two specific metals, one of which can absorb a large amount of hydrogen to form a stable hydride, while the other metal has a low affinity for hydrogen, but hydrogen can easily move in it. Mg, Ca, Ti, Zr, Y, and La belong to the first type of metal, and Fe, Co, Ni, Cr, Cu, and Zn belong to the second type of metal. The former controls the amount of hydrogen storage, and the latter controls the reversibility of the release of hydrogen. Through the reasonable preparation of the two, the hydrogen absorption and release performance of the alloy is adjusted, and a more ideal hydrogen storage material that can reversibly absorb and release hydrogen at room temperature is prepared.
3.Super heat-resistant alloy
Nickel-cobalt alloy can withstand high temperatures of 1,200 ℃ and can be used for components of jet aircraft and gas turbines. The nickel-cobalt-iron non-magnetic heat-resistant alloy still has the characteristics of high strength and good toughness at 1 200 ℃, and can be used for parts of space shuttles and control rods of atomic reactors. Searching for alloy materials that meet the requirements of high temperature resistance, long-term operation (over 10 000 h), corrosion resistance, and high strength is still the direction of future research.
4.Shape Memory Alloys
They have the characteristics of high elasticity, metal rubber performance, high strength, etc. After being subjected to plastic deformation under a relatively low temperature, they will be heated to return to the shape before heating. Such as Ni-Ti, Ag-Cd, Cu-Cd, Cu-Al-Ni, Cu-Al-Zn and other alloys, which can be used to adjust the elastic components of the device (such as clutches, throttle valves, temperature control elements, etc.), heat engines Materials, medical materials (orthodontic materials), etc.
The shape memory effect comes from a kind of thermoelastic martensite transformation. The general martensitic transformation as a method of quenching and strengthening steel is to heat the steel to a certain critical temperature for a period of time, and then quickly cool it, such as directly inserting it into cold water (called quenching), at which time the steel is transformed into one It has a martensitic structure and hardens the steel. Later, another so-called thermoelastic martensite transformation was found in some alloys. Once the thermoelastic martensite is produced, it can continue to grow as the temperature decreases. On the contrary, when the temperature rises, the grown-up martensite can shrink again until it returns to its original state, that is, the martensite can grow up or shrink reversibly as the temperature changes. The thermoelastic martensite transformation is accompanied by a change in shape.
In addition to the above-mentioned categories of new metal functional materials, there are also damping alloys that can reduce noise; biomedical materials that can replace, enhance and repair human organs and tissues; have implanted sensors, signal processors, and communications in materials or structures Together with controllers and actuators, the materials or structures can be self-diagnosed, self-adapted, and even damaged self-healing and other intelligent functions and life characteristics of intelligent materials.
Alloy Parts Manufacturing And Metal Cnc Machining
- [1] Medium carbon steel: representative steel grades are 30, 35, 40, 45, and also ML30, ML35, ML40, ML45, which have relatively stable room temperature performance and are used for small and medium structural parts, fasteners, drive shafts, gears, etc. .
- [2] Manganese steel: representative steel grades 40Mn2, 50Mn2. It has overheating sensitivity, high temperature tempering brittleness, water quenching is easy to crack, and the hardenability is higher than that of carbon steel.
- [3] Silicon-manganese steel: on behalf of the steel types 35SiMn, 42SiMn. High fatigue strength, decarburization and overheating sensitivity and temper brittleness. It is used to manufacture gears, shafts, shafts, connecting rods, worms, etc. with medium-speed, medium-to-high load and low impact. It can also manufacture fasteners below 400℃.
- [4] Boron steel: representative steel grades 40B, 45B, 50BA, ML35B. High hardenability, comprehensive mechanical properties higher than carbon steel, equivalent to 40Cr, used to manufacture parts and fasteners with small cross-sectional dimensions.
- [5] Manganese-boron steel: representative steel grade 40MnB. The hardenability is slightly higher than 40Cr, high strength, toughness and low temperature impact toughness, and temper brittleness. 40MnB is commonly used to replace 40Cr to make large cross-section parts and 40CrNi to make small parts; 45MnB replaces 40Cr and 45Cr; 45Mn2B replaces 45Cr and partly replaces 40CrNi and 45CrNi as important shafts. ML35 MnB is also used for fastener production.
- [6] Manganese vanadium boron steel: representative steel grades 20 MnVB, 40MnVB,. The quenching and tempering performance and hardenability are better than 40Cr, the tendency of overheating is small, and there is temper brittleness. It is often used to replace 40Cr, 45Cr, 38CrSi, 42CrMo and 40CrNi to manufacture important quenched and tempered parts, and ML20 MnVB with small and medium size bolts below 10.9 is also used.
- [7] Manganese tungsten boron steel: representative steel grade 40MnWB. Good low temperature impact performance, no temper brittleness. It is equivalent to 35CrMo and 40CrNi, used to manufacture parts below 70mm.
- [8] Silicon-manganese-molybdenum-tungsten steel: represents the steel type 35SiMn2MoW. It has high hardenability, calculated as 50% martensite, water quenching diameter is 180, oil quenching diameter is 100; the tendency of quenching cracking and tempering brittleness is small; it has high strength and high toughness. It can replace 35CrNiMoA and 40CrNiMo, and is used to manufacture shafts, connecting rods and bolts with large cross-sections and heavy loads.
- [9] Silicon-manganese-molybdenum-tungsten-vanadium steel: representative steel grade 37SiMn2MoWVA. Water quenching diameter 100, oil quenching diameter 70; good tempering stability, low-temperature impact toughness, higher high-temperature strength, temper brittleness is also small, used to manufacture large cross-section shaft parts.
- [10] Chrome steel: represented by 40Cr alloy steel pipe and ML40Cr. The hardenability is good, water quenching 28-60mm, oil quenching 15-40mm. High comprehensive mechanical properties, good low-temperature impact toughness, low notch sensitivity, and temper brittleness. Used to manufacture shafts, connecting rods, gears and bolts.
- [11] Chromium silicon steel: Representative steel grade 38CrSi. The hardenability is better than 40Cr, the strength and low-temperature impact are higher, the tempering stability is better, and the tempering brittleness tendency is greater. It is often used to manufacture 30-40mm shafts, bolts and gears with small modulus.
- [12] Chrome-molybdenum steel: representative steel grades 30CrMoA, 42CrMo, ML30CrMo, ML42CrMo. Water quenching 30-55mm, oil quenching 15-40mm; high room temperature mechanical properties and high high temperature strength, good low temperature impact; no temper brittleness. Used to manufacture parts with large cross-sections, high-load bolts, gears, flanges and bolts below 500°C; conduits and fasteners below 400°C. 42CrMo has higher hardenability than 30CrMoA and is used to manufacture parts with higher strength and larger cross-section.
- [13] Chromium-manganese-molybdenum steel: representative steel grade 40CrMnMo. The oil quenching diameter is 80mm, which has high comprehensive mechanical properties and good tempering stability. Used to manufacture heavy-duty gears and shaft parts with large cross-sections.
- [14] Manganese-molybdenum-vanadium steel: representative steel grade 30Mn2MoWA. It has good hardenability: water quenching reaches 150mm, the core structure is upper and lower bainite plus a small amount of martensite; oil quenching 70mm, the core is more than 95% martensite; good low-temperature impact toughness, low Notch sensitivity and higher fatigue strength. Used to manufacture important parts below 80mm.
- [15] Chromium-manganese-silicon steel: representative steel grade 30CrMnSiA. Water quenching 40-60mm (95% martensite), oil quenching 25-40mm. High strength, impact toughness, temper brittleness. Used to manufacture high-pressure blower blades, valve plates, clutch friction plates, shafts and gears, etc.
- [16] Chromium-nickel steel: Representative steel grades 40CrNi and 45CrNi. Water quenching reaches 40mm, oil quenching 15-25mm; good comprehensive mechanical properties, good low-temperature impact toughness, low temper brittleness tendency. 30CrNi3A has high hardenability, good comprehensive mechanical properties, white spot sensitivity and temper brittleness. Used to manufacture crankshafts, connecting rods, gears, shafts and bolts with large cross-sections.
- [17] Chromium-nickel-molybdenum steel: representative steel grade 40CrNiMoA. It has excellent comprehensive mechanical properties, high low-temperature impact toughness, low notch sensitivity, and no temper brittleness. It is used to manufacture large crankshafts, shafts, connecting rods, gears, bolts and other parts with large forces and complex shapes.
- [18] Chromium-nickel-molybdenum-vanadium steel: Representative steel grade 45CrNiMoVA. High strength, good tempering stability, oil quenching up to 60mm (95% martensite). It is used to manufacture elastic shafts and torsion shafts of heavy-duty vehicles under vibration load.
The Castingproperty Of Alloy
The casting performance of an alloy refers to the process performance of the alloy during casting, mainly refers to the fluidity of the alloy and the shrinkage of the alloy. These properties are very important for obtaining sound castings.
1.Liquidity
Liquidity refers to the ability of liquid alloy to fill the mold.
The fluidity of the alloy liquid is good, and it is easy to fill the cavity to obtain castings with clear contours and complete dimensions. On the contrary, if the fluidity of the alloy is not good, defects such as insufficient pouring, cold barrier, pores and slag inclusion are easy to occur.
Among the commonly used alloys, gray cast iron and silicon brass have the best fluidity, and cast steel has the worst fluidity.
There are many factors that affect fluidity, among which are the chemical composition of the alloy, the pouring temperature and the filling conditions of the mold.
2.Shrinkage
The phenomenon that the volume and size of the liquid alloy continue to decrease during the cooling and solidification process is called shrinkage. Shrinkage is the physical property of the casting alloy itself, and it is the basic cause of many defects (shrinkage cavity, shrinkage porosity, internal stress, deformation and cracks, etc.) in the casting. The alloy liquid goes through three stages from pouring into the cavity to cool down to room temperature:
- liquidcontraction: the contraction between the cooling of the pouring temperature and the liquidus temperature at which crystallization begins.
- Solidificationcontraction: the contraction from the cooling of the starting crystallization temperature to the solidus temperature at which the crystallization is completed.
- solidcontraction: the contraction from the temperature at which the crystallization is completed to the room temperature.
The liquid shrinkage and solidification shrinkage of the alloy are manifested as the volume reduction of the alloy, which is usually expressed by the volume shrinkage rate. They are the basic reasons for the shrinkage cavity and shrinkage defects of the casting. Although the solid-state shrinkage of the alloy is also a volume change, it only causes a change in the outer dimensions of the casting. Therefore, it is usually expressed by the linear shrinkage rate. Solid state shrinkage is the root cause of defects such as internal stress, deformation and cracks in castings.
The chemical composition of the alloy, pouring temperature, mold conditions and casting structure are the main factors affecting alloy shrinkage. The shape, size and process conditions of the casting are different, and the actual shrinkage is also different.
In addition, the uneven chemical composition of each part of the alloy liquid in the process of cooling into a casting, that is, segregation, gas absorption and oxidation have an adverse effect on the casting performance.
Link to this article:Alloy Definition
Reprint Statement: If there are no special instructions, all articles on this site are original. Please indicate the source for reprinting:Alloy Wiki,thanks!^^