Wax pattern making is a key link in the precision casting process. The quality of the wax pattern will directly affect the quality of the casting. The following are the common defects of wax patterns and their solutions summarized by our factory technicians:
- Wax pattern deformation. After the wax pattern is taken out from the mold, in addition to the reduction in size, sometimes artificial deformation occurs due to improper handling during removal; since it is common for the wax pattern to flex and deform during cooling, so the wax mold that has just been taken out from the molding process must still be placed carefully. It is usually placed flat with a larger plane as the reference plane. Or put them in a big cooling tank. In addition, it may be caused by factors such as the wax material being too soft or the molding design being unreasonable.
2. The wax mold is not fully filled. The main reason is that the temperature of the wax material is too low, the injection speed is slow, or the molding temperature is low, causing the wax material to cool quickly during the flow process, which is manifested in the corners and edges or the thinness of the wax mold. The wall part is not fully filled, and rounded corners appear. This situation is very similar to insufficient pouring of metal castings.
3. Wrinkles on the surface of the wax mold:It is due to too low temperature of the wax material, too low shooting speed, improper coordination of wax movement and molding temperature; or due to damage or uncleanness of the inner surface of the molding; improper placement of the chilled metal block, etc. It left traces of movement on the surface of the wax pattern. Deeper lines are similar to the cold-shut defect of metal castings; there are also seams sometimes visible around the core and around the holes, which are slightly sunken. In fact, the meeting point of the two wax flows fails to fuse well. It is the result of insufficient temperature and insufficient pressure of the wax material.
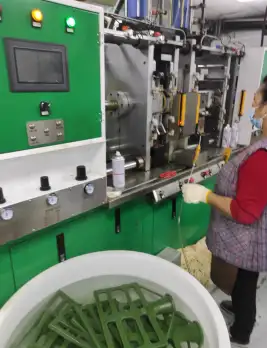
4. The surface of the wax mold is sunken: It is mainly due to insufficient injection pressure and time, or high temperature of the wax material with insufficient cooling time, and sometimes too much release agent. If the surface sunken involves a large area, It will make repair difficult and easy to cause scrap.
5. There are gaps in the wax mold. This is the most common defect. Thin wax flakes may escape at the junction of the molding assembly block, the connection between the core and the core seat, and other connection areas during the molding process. The main reasons are that the molding accuracy is not enough, the molding parting surface or the joint surface of the internal parts of the mold is damaged or dirt is attached, or the molding force is not enough, the injection pressure is too high, etc. Or the temperature of the wax is too high. The burrs must be completely removed before the wax mold can be used.
6. The wax mold adheres to the mold. This is because no release agent is used, or the temperature of the wax and the mold is too high, or the inner surface of the mold is not clean enough.
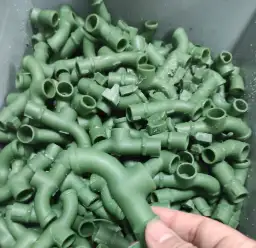
7. The surface of the wax mold is rough. Due to the low injection pressure or low injection speed, the contact density between the wax material and the inner surface of the mold is insufficient, and wrinkles may occur in severe cases.
8. There are bubbles in the wax model. One is the bubbles on the surface that are visible to the naked eye. The other is the bubbles inside the wax model. They are usually large and cannot be seen with the naked eye, but they can be found through the local bulging of the wax model. This is caused by the expansion of gas within the wax pattern.
Disclaimer: Some of the content in this article is reproduced online, and the copyright belongs to the original author. If there are any copyright issues related to the work, please contact us. We will confirm the copyright based on the copyright proof materials you provide and delete or take relevant measures within one week of receiving the proof!
Link to this article:Common defects of wax patterns in precision casting and their solutions
Reprint Statement: If there are no special instructions, all articles on this site are original. Please indicate the source for reprinting:Alloy Wiki,thanks!^^